Waterproof membranes - Wykamol installation guide
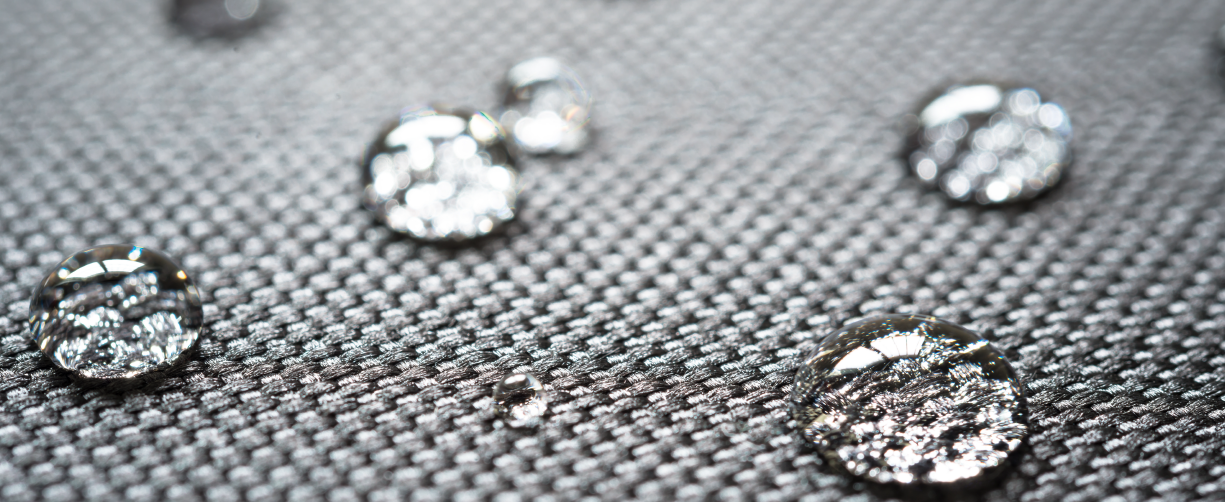
The Wykamol Group has been involved in waterproofing applications for over 40 years and was a founder member of the British Wood Preserving and Damp Proofing Association. When it comes to waterproofing applications, the Wykamol Group has a huge range of products, from cement-based tanking powders to specialist epoxy coatings. In recent times however and since the changes to BS8102, cavity drain membranes have fast become the choice for most contractors in the UK marketplace.
CM8- Waterproof membrane
For use on walls, floors, vaults and tunnels with minimal surface preparation required. Also suitable for external foundation waterproofing and to provide
insulated dry lining for walls above ground level that may not be suitable for conventional plaster finishes.
Wykamol CM membranes are suitable for use in type ‘C’ (drained protection) structural
concrete constructions in accordance with BS 8102:1990, clause 3.2.4.
Wykamol CM8 is a medium capacity drainage membrane (4 litres/m2) for floors and walls both above andbelow ground level.
When used on basement floors it is recommended that perimeter drainage channels are provided to optimise the flow of ground water towards the sump location (see separate data sheet ‘Wykamol Drainage Solutions’).
Wykamol CM8 is used in a dry lining application. Various systems can be used in the head of the fixing plug, from timber battens to steel dry lining systems.
This membrane is easy to roll out against wall and floor structures and can be fixed in horizontal lengths or in vertical strips. This is our most popular membrane in
basement waterproofing due to its universal ease of use.
FIXING
Wykamol CM8 Membrane is installed with studs against the underlying structure. Fixing to walls is carried out with Wykamol Brick Plug in the centre of the stud. Take care when drilling holes to avoid excessive masonry dust falling in to the cavity.
• Can create a dry habitable living space in areas previously suffering from damp/wet conditions.
• Little to no damage to existing structure.
• Quick to install- minimal preparation needed to wall surfaces, avoiding mess and saving time and money.
• Easy to bend and cut with scissors to form around windows, doors, services etc.
• No delays to decoration as there is no drying process.
• Waterproof, salt resistant, root resistant and contaminant resistant
• Low and high temperature tolerance.
KONTRACT MESH- plaster membrane
Kontract Mesh is suitable for use in accordance with BS 8102:1990 to provide Type ‘C’ drained protection to structures below ground giving a
Grade 3 or 4 dry environment suitable for domestic or commercial use.
Kontract Mesh is a high density polyethylene membrane, incorporating 8 mm studs which allows the isolation of wet walls above
and below ground. It incorporates a tough HDPE mesh lathing welded to the front face to allow the direct application of various plaster finishes or adhesive ‘dabs’ and plasterboard. Note: in basements where the walls are particularly wet (running water) we recommend the use of Kontract 8 on walls and floors (see separate data sheet).
FIXING
Kontract Mesh is fixed to the wall by drilling through the membrane studs to a depth of 50 or 70mm using a 8 mm drill bit, and gently hammering home the Plaster Plugs with seals to form a waterproof seal between the fixing and the membrane surface. Alternatively, Plaster Plugs with Wykamol Rope around the shaft can be used. Intervals
between plug fixings should be no greater than 250mm to ensure a tight fix to the wall. Near lap joints and where the surface is uneven, the centres should be less than 250mm. When fixing the membrane it is essential to keep the sheet tight to the wall surface (no ‘bulges’) at all times.
• Stud height 8 mm, drainage volume 5.5 litres/m2
• Sheet thickness 600 _m, density 0.7 kg/m2
• Excellent low and high temperature stability
• 150 kN/m2 load bearing capacity
• High durability and water resistance
CM8 & KONTRACT 8 - wall aplication
PREPARATION
Wykamol wall membrane can be installed over a wide range of substrates in varying situations - walls, floors, ceilings, soffits, etc. However, before the System is installed, the area must be assessed to determine what preparation is required:
a) All timber fixtures and other organic material must be removed to prevent risk of fungal or bacterial growth behind the System, e.g. skirting boards, timber plates, old wallpaper etc. Structural repairs or works to remove items likely to puncture the membrane must be carried out. If evidence of rot or mould exists, this should be treated. (Wykamol Microtech Biocide, Wykabor 10 or Mould Clear Concentrate)
b) If the walls are uneven or areas have deteriorated, any large depressions should be levelled and made good to ensure a solid fixing.
c) When assessing floor applications, consideration should be given to the type of finish that is required. The floor must be cleared of oil, loose material and any sharp edges should be levelled out. Any holes or severe depressions should be filled. When a timber floor is preferred, then more consideration should be given to achieve a flat substrate prior to laying the membrane. This will relieve any undue movement when fitting a final floor finish.
d) The design of the drainage system should be agreed, implemented and tested before covering by the membrane. The exception to this is where the Aqua Channel is sat above the slab or raft. Flood tests should be made to check the slab or raft is flat and level prior to the installation of the Aqua Channel, but the system can
only be fully tested once the floor membrane and some form of resistance to water pressure is placed above the membrane such as temporary boards with bags of ballast or sand placed above, or the finished floor covering.
e) When fixing the system to flat soffits you must ensure that there is a fall to create proper drainage and prevent ponding. Any sagging of the membrane should not be great enough for ponding to take place.
TOOLS
Minimum Required:
• Good quality 110V SDS hammer drill
• Mallet or club hammer
• Stanley Knife with spare blades
• Cutting shears
• Tape measure
• Long spirit level
• 8mm & 10mm SDS drill bits
• Clean rags
• Trestle staging or scaffold for working
at height
Recommended
• Extra lighting
• Hot Air Gun
WALL APPLICATION
The Wykamol wall membrane is fixed with the studs against the wall to create an air/depressurisation gap. The membrane can be fixed either vertically or horizontally. When making this decision, you will need to take into account the size of the area to be lined, and the height of the walls relative to the width of the membrane. Horizontal
fixing requires fewer cuts and jointing but the full roll is very heavy at first. Vertical fixing has very much lighter strips to fix, but requires that each of these is taped back together again. You may find that vertical fixing is easier, but requires more Corner Detail Tape for jointing. The membrane is fixed to the wall using
a Brick Plug fixing. The Brick Plug should have a waterproof seal applied to the collar using a soft rubber sealing washer or Wykamol Rope fitted to the plug for sealing to the wall membrane. Place the wall membrane in position as level as you can judge by eye. Using a 10mm drill bit, drill through the centre of a stud near the top and
edge to a depth greater than the fixing. The fixing is then hammered into the pre-drilled hole until the plug sits flush in the stud. The rubber washer reseals the hole. Level the membrane using the spirit level or laser level if used, and fix another plug about 2m along at the top of the sheet. The membrane will now be hanging level to the wall. If you are fixing horizontally, continue fixing every 2m until you have reached the end of the roll or you have covered all of the wall(s) to be treated. It is very important to regularly check the level. If the membrane is not level, you may well find that the membrane is kinked and looks unsightly, it will also dive down when fitted around corners. If you are fixing vertically, hang each subsequent sheet by the two fixings as described above. The subsequent sheet should overlap by at least the width of the flange of the new sheet. You may find it easier to interlock the first stud of the new sheet to the last stud of the last sheet as this helps to keep the new sheet level. The vertical joints have to be sealed with Wykamol Tape. It is easier to apply the tape to the inner surface of the flange of the next sheet. Clean the flange
and the face of the last sheet with a clean rag. When you have fixed the new sheet level with the correct overlap, pull off the backing paper from the tape and peel down whilst applying pressure to the flange. Once all the backing paper has been removed, apply more pressure with the palm of your hand to further seal the whole of the joint. A Hot Air Gun should be used to help sealing in cold or damp conditions.
FIXING CENTRES
Once the Wykamol membrane is hanging off the top fixings the rest of the fixing plugs need to be fixed.
The spacing of these fixings is dependent on the type of wall finish to be used:
• Timber battens 400mm centres vertically and 600mm horizontally. Barrel Vaults require tighter centres.
• Fixed metal track (Gypliner) 600mm centres vertically and 800mm horizontally. Brick or block walls restrained to
the retaining wall using ties should have the fixings at centres to provide the correct number of restraints at the correct centres. Free standing timber and metal frames and free standing block walls do not require specific fixing centres. In these cases use sufficient fixings to ensure the membrane is neat and tidy and reasonably tight to the wall, especially around corners and reveals. When fixing the system to flat soffits you must ensure that enough fixings are used to keep the membrane tight to the soffits with no sagging. All fixings should be in line both horizontally and vertically.
BATTENS
Battens should be pre-treated and of a minimum dimension of 25mm x 38mm although you may find that 25mm x 50mm offers better fixing at the edge of the plasterboard. The battens can be fixed into the fixing plugs without piercing the membrane, by using 5mm (size 10) self-tapping screws. The plug will take
30mm of screw, so be sure to purchase the correct length for the thickness of batten. Over-tightening of over length screws can loosen the plug. Be very careful not to puncture the membrane when drilling and fixing the battens. Battens should be fixed so that all plasterboard edges are supported. Use a timber treated batten or treat
with a preservative. (Wykabor Cut End) to protect cut battens. Once the battens are fitted into position, plasterboard can be fixed to them using clout nails or preferably plasterboard screws. Care should be taken not to exceed the depth of the battens with the screws, and thereby puncture the membrane.
ALTERNATIVE FIXINGS
Other finishes may be employed depending on the requirements of the specifier.
a) FREE STANDING FRAME This method should be employed if the wall is undulating, as with some stone structures or where space loss is a secondary consideration. The frame would be fixed to the soffit and the floor finish with the supplied 'U' channels. With the increasing requirement of insulation to meet Part 'L' of building code, the use of these frames in becoming more popular, the thickness of insulation required is often in excess of the thickness of the frame, and so no wall thickness is not lost when using this method. Because the frame is free standing and has no relationship with the wall membrane, very few fixings are required and so this wall finish above allows for the fastest and most efficient method of fixing membrane to the wall.
b) PROPRIETARY FIXING SYSTEMS Fixing systems such as Gypliner or Lafarge can be used with Wykamol membrane. It is also possible to use metal profile systems when constructing new internal walls. These can be fixed without bridging the membrane.
c) INTERNAL BLOCK WALLS If preferred the system can provide a water and vapour proof barrier, and then be lined with a block or brick inner skin.
SERVICES
If there are any services through the wall and floor, the membrane can be cut and trimmed around them and the gap filled and sealed using
Wykamol Rope and Corner Detail Tape. If necessary, a patch of membrane or plain DPC (PVC) is laid over and sealed to the service
with Wykamol Rope and around its perimeter with Corner Detail Tape. It should be noted that protrusions through the floor slab/raft should be avoided wherever possible as they create weaknesses that allow unnecessary water ingress. The specified floor finish can now be laid directly over the floor membrane, which must not be punctured by any fixings through the floor. When a timber floor finish is preferred you must allow an expansion gap around the wall edge. Speak to the supplier of the
floor finish to confirm the correct size of this expansion gap.
GENERAL
Occasionally, service pipes and other intrusions will interrupt a continuous application of the membrane. In this instance the membrane should
be trimmed neatly around the service and sealed using the Wykamol Rope or Corner Detail Tape, or if necessary a combination of both.
CM8 & KONTRACT 8 - floor aplication
PREPARATION
Please refer to our section on preparation and attend to any preparatory work prior to installation. Always clean both edges of the membrane before making a seal.
DRAINAGE REQUIREMENT
If CM8 or Kontract 8 is to be used in a full or part earth-retaining situation, the membrane system must be drained. To comply with BS8102, you must assume that the structure will be subjected to water ingress at some time. CM8 and Kontract 8 can also be used on the floor in above ground situations to provide isolation from damp floors either as the primary DPM or above green concrete to accelerate the contract program. The concrete will continue to cure below the dry membrane surface allowing
for floor finishes to be laid above the membrane much quicker than normal.
METHODS OF DRAINAGE FOR CM8 & KONTRACT 8 TO THE FLOOR
The drainage must effectively remove all water from below the membrane and take the water to a point of discharge such as a sump chamber
or a form of safe natural drainage. Standing water can block the membrane with silt or lime scale so it is important for water to flow uninterrupted to
the drainage point.
AQUA DRAIN & AQUA CHANNEL Aqua Drain & Aqua Channel sits in at the wall/floor junction and collects water from behind the wall membrane and receives water at the wall / floor junction. They are a designed method of removing water as it can interface with sump chambers, stack pipes, gullies, waste pipes etc. Aqua Channel can be serviced by inserting jetting eyes into the system.
CENTRAL DRAINAGE When a new slab is being laid this presents the opportunity to install a Central Drainage system. A network of 100mm pipe work laid to evacuate water from the slab to a groundwater sump chamber. Please refer to our Technical Drawings guide. A silification treatment should be applied to new slabs. This will lock in free limes present within the slab. (Wykamol Microseal)
INSTALLATION OF CM8 & KONTRACT 8 TO THE FLOOR
Starting at one side of the room, unroll the membrane with the studs down and cut to fit the room as one would a carpet. The next membrane width is rolled out so that the flanged edge overlaps onto the edge of the previous roll of membrane. Clean both edges. Wykamol Tape is then applied to the edge of previous roll of membrane with the backing paper still intact. Check the two widths for alignment, with the flange covering the backing paper. Starting from the middle of the joint, remove
the backing paper and press down on the joint sealing the two sections together. This process is repeated until all areas are covered. Seal the floor membrane to the wall membrane using Corner Detail Tape. Refer to Technical Drawings guide. Where the floor membrane is required to be jointed to horizontal DPC s through internal and
external walls, these joints should be sealed with Wykamol Corner Detail Tape. Ensure both surfaces are clean and dry before attempting to make these joints. If there are
any services up through the floor, the membrane can be cut and trimmed around them, and the gap filled and sealed using the Wykamol range of tapes. If necessary, a patch of membrane or plain DPC (PVC) is laid over and sealed to the service with Wykamol Rope and around its perimeter with Corner Detaill Tape. It should be noted that protrusions through the floor slab should be avoided wherever possible as they create weaknesses that allow unnecessary water ingress. The specified floor finish can now be laid directly over the floor membrane, which must not be punctured by any fixings through the floor. When a timber floor finish is preferred you must allow an expansion gap around the wall edge. Speak to the supplier of the floor finish to confirm the correct size of this expansion gap.
Source: WYKAMOL